Free shipping over $99!
Diagnosing a Blowing Fuse: A Step-by-Step Guide to Tube Amp Troubleshooting
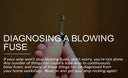
Diagnosing a Blowing Fuse: A Step-by-Step Guide to Tube Amp Troubleshooting
Published on
January 21st, 2021
Welcome back to another installment of Mojotone’s Fix It Friday series. Today, I’ll be working alongside high wizard of amplification and Mojotone Allstar, Steve Snyder, in an effort to diagnose a repetitive fuse-blowing issue in my Deluxe Reverb.
If you are running into, or have ever run into, an issue with constantly blowing a fuse, you are certainly not alone. There are a number of things that could be happening inside the amp to cause this, so today we are going to walk through a few of the basic troubleshooting points to help you narrow down, or even pinpoint, the problem.
Here is a short list of tools and supplies you'll need to get going:
or drill
The first thing we want to do is check the actual fuse itself. Often times, fuse values will get mixed up and you could have received an improper value. Likewise, sometimes fuses are just bad from the factory, so you want to make sure the fuse is working properly to begin with. The easiest way to do this is to grab your multimeter and test for resistance across the fuse. To do this, place one multimeter probe on each of the metal tabs on either end of the fuse (Image 1A).
We are hoping to see a reading as close to ‘0’ as possible. My current fuse looks good, so now we can test the next thing in line, which in this case would be our tubes.
We will start by turning the amp to ‘ON’ without flipping the STANDBY switch. Now we will need to watch and see what happens. If the fuse blows here, you could be looking at one of a few things:
1) Your rectifier tube could be going bad, and you will need to test this by inserting a new rectifier tube, as well as a working fuse, and watching to see if the problem persists.
2) Some amps charge one or more filter caps in the ‘ON’ position, so there could be a faulty filter cap involved. A way to test this is to remove the rectifier tube, replace the fuse and see if the issue continues.
3) You may have a bad filament in another tube somewhere downstream. To test for this, you would remove the rectifier tube, replace the fuse, turn the amp ‘ON’ and watch to see if one or more of your tubes is NOT glowing.
If none of the above checkpoints indicate a problem, we can proceed. The next thing to look for, and a very likely culprit, is red plating in the power tubes. To test for this, we will insert a working fuse, turn the amp to the ‘ON’ position, allow the amp to warm up for 60 seconds, and then flip the STANDBY switch. Looking at your power tubes, check the area highlighted in Image 2A below.

The above image is of a normal functioning tube. For an example of true red plating, take a look at Image 3A below and notice the cherry red glow on the tube’s plate.

While the above image is a good example of an obvious red plate, sometimes overheating in tubes is not quite as apparent. You’ll want to make sure nothing smells like it is burning; you may even feel the heat coming off the tubes without actually touching (as this could burn you depending on how hot they get); even check the screen-printed graphics on the tube (if there are any) to make sure they haven’t been burned away, as in Image 4A below…
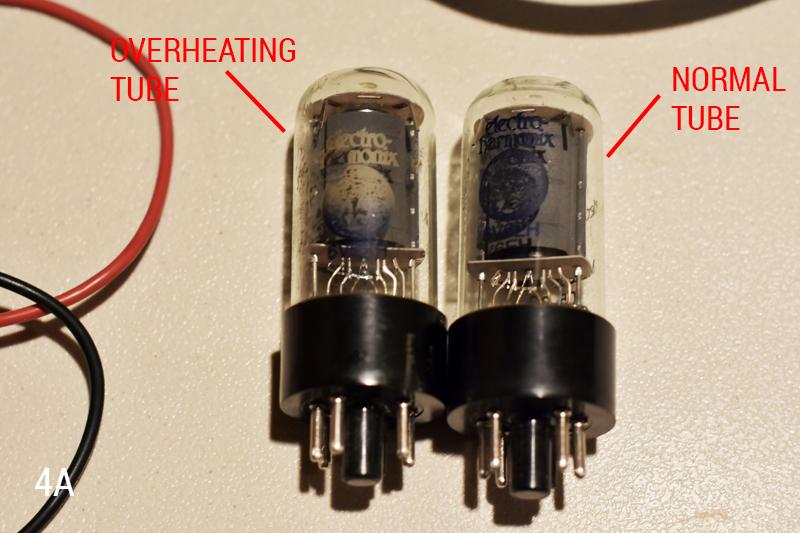
If you find that a power tube is red plating, the first test should be to switch the sockets of your power tubes to see if the red plating follows the tube or stays with the socket. If the red plating stays with the same tube regardless of the socket, you will know it is an issue with the tube itself and in all likelihood a new matched pair of tubes should do the trick. If the red plating stays with the socket regardless of which tube is inserted, the issue goes deeper.
Note: For today’s demonstration we will only be able go so far, as this rabbit hole could potentially go quite deep and may eventually require a certified technician. For now, however, we should be able to remove our chassis and test for a couple of things.
If we suspect our tube socket is the issue, we will need to test the tube socket’s negative bias voltage. In order to do so, we will need to test pin 5 on the suspected tube socket. This will require us to use our multimeters set to DC voltage; attach the negative multimeter probe to the chassis (ground) and use ONE HAND to place the positive multimeter probe on pin 5 (Image 5A).

Note: To safely perform this test, the amp will need to be switched to the ‘ON’ position, with a speaker load connected.
As you can see, pin 5 on my amp is reading -39V, which means it is getting an acceptable negative bias voltage (this number will vary per amplifier and can also have a +/- 5V tolerance). If you are reading 0V, however, you now know there is an issue in this area. If your amp has a resistor running from pin 5 to another pin on the socket, you will need to test voltage at the other end of said resistor. If you are receiving acceptable voltage on the other end of the resistor, you know the resistor is bad and needs to be replaced (Image 6A for more detail).

If you are still getting a 0V reading at this point, we can go a bit deeper. Now we need to know where this bias is coming from, so we can either follow the wire coming from this pin visually, or use our wiring diagrams/schematics to see where this connection leads. In my case, the wire from my socket is leading to the point on my board highlighted in Image 7A below…

Perform the same voltage meter test here as we did above. If you are getting a good reading at this point, it means the issue is the connection between the board and the socket. This will require double-checking the solder joint and potentially replacing the connector wire.
If, however, you are not getting a reading at this point, you should be able to replace the resistor highlighted in Image 8A below. If, for any reason, the replacement of this resistor is ineffective, you will need to contact a certified amp technician to take a closer look.

As we know, any number of things can go wrong in a tube amp; it’s just the nature of the beast. Our tutorials are aimed towards entry-level DIYers, and sometimes we can only go so far with safety and certainty in mind. As it turns out, the issue with MY amp today was, in fact, red plating. I swapped my tubes and found that the issue followed the tube rather than the socket. Lucky for me I was able to try out a new set of tubes and everything went back to normal.
We hope you found this tutorial helpful, and hopefully this will get you one step closer to becoming self-sufficient when it comes to amp maintenance and repair. Please join us next month for another project!
Before we get started, I'll need you all to read the following...
DISCLAIMER:
MANY OF THE FOLLOWING DIAGNOSTIC PROCEDURES REQUIRE WORKING WITH DANGEROUS AND POTENTIALLY LETHAL VOLTAGES. MOJOTONE IS NOT RESPONSIBLE FOR ANY INJURIES INCURRED WHILE FOLLOWING ALONG WITH THIS ARTICLE. IN ORDER TO PROTECT YOURSELF FROM HARM, PLEASE TAKE ALL NECESSARY SAFETY PRECAUTIONS WHILE WORKING ON YOUR AMPLIFIER.


The above image is of a normal functioning tube. For an example of true red plating, take a look at Image 3A below and notice the cherry red glow on the tube’s plate.

While the above image is a good example of an obvious red plate, sometimes overheating in tubes is not quite as apparent. You’ll want to make sure nothing smells like it is burning; you may even feel the heat coming off the tubes without actually touching (as this could burn you depending on how hot they get); even check the screen-printed graphics on the tube (if there are any) to make sure they haven’t been burned away, as in Image 4A below…
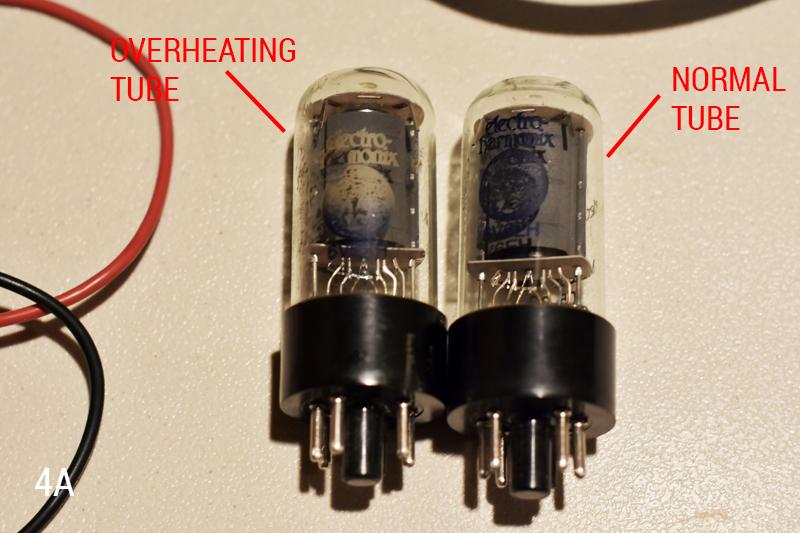
If you find that a power tube is red plating, the first test should be to switch the sockets of your power tubes to see if the red plating follows the tube or stays with the socket. If the red plating stays with the same tube regardless of the socket, you will know it is an issue with the tube itself and in all likelihood a new matched pair of tubes should do the trick. If the red plating stays with the socket regardless of which tube is inserted, the issue goes deeper.
Note: For today’s demonstration we will only be able go so far, as this rabbit hole could potentially go quite deep and may eventually require a certified technician. For now, however, we should be able to remove our chassis and test for a couple of things.
If we suspect our tube socket is the issue, we will need to test the tube socket’s negative bias voltage. In order to do so, we will need to test pin 5 on the suspected tube socket. This will require us to use our multimeters set to DC voltage; attach the negative multimeter probe to the chassis (ground) and use ONE HAND to place the positive multimeter probe on pin 5 (Image 5A).

Note: To safely perform this test, the amp will need to be switched to the ‘ON’ position, with a speaker load connected.
As you can see, pin 5 on my amp is reading -39V, which means it is getting an acceptable negative bias voltage (this number will vary per amplifier and can also have a +/- 5V tolerance). If you are reading 0V, however, you now know there is an issue in this area. If your amp has a resistor running from pin 5 to another pin on the socket, you will need to test voltage at the other end of said resistor. If you are receiving acceptable voltage on the other end of the resistor, you know the resistor is bad and needs to be replaced (Image 6A for more detail).

If you are still getting a 0V reading at this point, we can go a bit deeper. Now we need to know where this bias is coming from, so we can either follow the wire coming from this pin visually, or use our wiring diagrams/schematics to see where this connection leads. In my case, the wire from my socket is leading to the point on my board highlighted in Image 7A below…

Perform the same voltage meter test here as we did above. If you are getting a good reading at this point, it means the issue is the connection between the board and the socket. This will require double-checking the solder joint and potentially replacing the connector wire.
If, however, you are not getting a reading at this point, you should be able to replace the resistor highlighted in Image 8A below. If, for any reason, the replacement of this resistor is ineffective, you will need to contact a certified amp technician to take a closer look.

As we know, any number of things can go wrong in a tube amp; it’s just the nature of the beast. Our tutorials are aimed towards entry-level DIYers, and sometimes we can only go so far with safety and certainty in mind. As it turns out, the issue with MY amp today was, in fact, red plating. I swapped my tubes and found that the issue followed the tube rather than the socket. Lucky for me I was able to try out a new set of tubes and everything went back to normal.
We hope you found this tutorial helpful, and hopefully this will get you one step closer to becoming self-sufficient when it comes to amp maintenance and repair. Please join us next month for another project!